Company Restores Hydropower Plant on Sugar River in Claremont
Published: 05-22-2017 12:38 PM |
Claremont
Next to the dam, along the riverbank off Lafayette Street, Bob King stands on a large steel grate. Beneath him the water is calm as it flows into a concrete bay and through a 25-foot-deep “trash rack” that screens out large debris, to an underwater 10-foot diameter penstock. The penstock will carry the water 750 feet downstream to a hydroelectric plant that King and his partner bought earlier this year. By next month, King hopes to be harnessing some of that raw water power to produce electricity for Green Mountain Power’s nearby substation.
Watching the river’s fury, King can’t help but smile.
“The way it is running today, if we could use all that power, it would be about 4 megawatts. That river is surging. We could not use all that even with both units running.”
When the twin turbine hydroelectric plant, bought by Sugar River Power LLC in January, is operating at full capacity, it is capable of generating 1.35 megawatts of power — enough to power 1,300 homes, King said.
When John Webster built the Lower Village Hydro Dam in 1995, King said, he replaced an old dam and bypassed another with the penstock, which created a 40-foot drop, or “head,” from the intake to where the water exit’s the plant.
“He took the drop of two dams and combined it into one and that is how he got 40 feet of head,” King said. “That is pretty darn good for New England. The power produced is proportional to the drop.”
King has been captivated by hydropower since childhood and his latest acquisition in Claremont is the fifth small plant he and his partner, Tim Taylor, along with some other partners, own and operate. They also own three in the Keene area, where King lives, and one in western Massachusetts.
Article continues after...
Yesterday's Most Read Articles
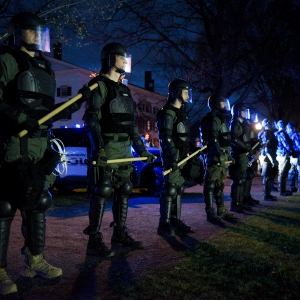
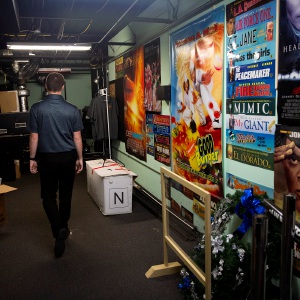

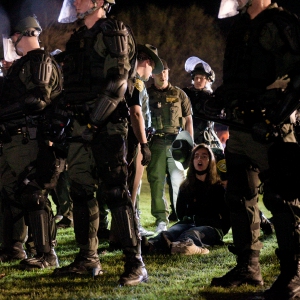

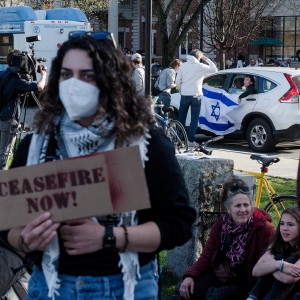
“I was bitten by the hydro bug when I was 11 years old in 1972, when I stumbled on an old abandoned plant in Massachusetts,” King said. “People were just beginning to talk about the energy crisis. Really smart people were beginning to think about climate change.
“As a kid I thought, wow, small hydro, this is the solution. Right there I just latched on to it.” He later went to college at Cornell, where a hydro plant was being rebuilt.
A Few Surprises
The Sugar River plant last operated in 2011. King’s company bought it in early January for $850,000, according to the city’s assessing records.
The purchase was finalized after the City Council approved a 10-year payment-in-lieu-of-taxes program, which is based on a percentage of gross revenues, not assessed value. In years one through four, the payment would be 2.5 percent of gross revenues; in years five through eight it would be 3.5 percent; and 5 percent for years nine and 10.
When he requested the payment program, King told the council he has an eight-year power purchase agreement with Green Mountain Power to sell what the plant produces for 8 cents a kilowatt-hour.
“What is great about Sugar River Power is this is locally produced renewable power that is going to benefit our customers,” Kristin Carlson, Vice President of Strategic and External Affairs with Green Mountain Power, said Friday. “We are committed to reducing power from carbon and this is an important part of that.”
At the plant last week, King, Taylor and a third employee, Sam Payne, were continuing refurbishing work on the facility’s mechanical pieces that they started in the dead of winter.
“We actually started in September sort of tinkering with permission for the owner as we worked out terms of the deal.” King said. “Then everything started in earnest in January.”
In December, King told the City Council that, because it had been offline for six years, the plant was “a real mess” and would require a significant investment of time and money before it was operational.
“We found quite a few surprises,” Kings said, comparing it to buying an old house and continuing to find more things that need attention. “We had to go through all sorts of technical challenges.”
Added to that was working through the bureaucracy to regain permission from ISO New England Inc., the Hadley, Mass.-based operator of the region’s bulk power system and wholesale electricity markets, for the plant to produce power for the grid. When the plant had shutdown, ISO dropped it from its system of energy producers, King said.
“It was a huge nightmare to get it back into the ISO system. You can’t go online without the ISO’s permission. They control the grid for all of New England.”
After finally arranging a meeting to plead their case, and with the help of Eversource, “ISO finally came around,” King said.
Eversource spokesman Martin Murray said Friday one of their roles is to help power producers navigate the rule and regulations.
“ISO is really a gatekeeper to ensure reliable transmission of energy throughout New England,” Murray said.
“Even small (power producers) are part of the six-state power grid. They need to be aware of any source that will be potentially part of that transmission.”
Eversource has nine hydro facilities of its own and buys power from about 30 statewide, Murray said. “We deal a lot with the regulations of ISO.”
Power Conversion
When he became serious about buying the plant last summer, King said, the first thing that had to be done was to rebuild one of the 10-foot-square steel gates that slide up to open the penstock.
“We couldn’t even close it to work on the plant until we completely rebuilt it because it was rusted and had collapsed into the penstock,” King said.
At the plant, a 1,500-square-foot building with a peaked roof, King explained how water and turbines combine to produce power.
As the penstock approaches the plant, it splits into two, 6-foot diameter pipes. A large butterfly valve can be adjusted to control the flow of the water as it moves through each pipe. Inside the building, the pipe turns downward at a 45 degree angle and the water passes through a turbine before exiting into the river.
The turbine, which King likened to a ship’s propeller, turns a 20-foot-long steel shaft that comes out of the pipe to a coupling connected to a gear box.
“The gears speed up a smaller spinning shaft that actually drives the electric generator (that sits above the shafts), which turns all that torque and power into electricity,” King said. “It basically converts mechanical energy into electrical energy.”
Reconditioning was gear box and getting it properly aligned has proven to be the toughest and most time-consuming challenge, King said.
“Gear boxes are notoriously finicky and they require precise alignment and they have lubrication systems. The bearings were all shot in that thing, almost everything about it needed to be reworked,” King said.
“Aligning the turbine shaft to the gear box shaft took weeks. We actually had to cut parts of that tank away and reweld it. Everything was so far out of alignment. You are shooting for alignment within a 5,000th of an inch. We found some things that were an inch out, just way off.”
The shaft on the second turbine generator, closest to the river, was spinning — but not to produce electricity.
“We are just idling it to slowly move sand out of the bottom end. That one (turbine generator) needs to be rebuilt completely even more than this one,” King said. “But before we can rebuild it, we have to drop a gate in the back where it exits into the river and then pump it out so we can work on it. We can’t even do that until we get the sand out of the exit tunnel.”
Powering the Past, And the Future
The technology to harness water power, and how that power is used, has changed dramatically the last 250 years since Benjamin Tyler built Claremont’s first water-powered mill on the Sugar River in the 1760s in the area of the former Coy Paper property on Plains Road.
But what Tyler did then, and what Sugar River Power is doing today, has not changed — figuring out the most efficient way to turn rushing water into power, whether to run saw mills and grist mills or electric lights and computers.
Water power fueled Claremont’s expansive growth from the mid-1800s into the 20th century. Most of that growth was in a three-quarter mile stretch of river through the heart of the downtown, but included mills in West Claremont as well. Valuable dam privileges along the river created well-known companies including Sullivan Machine and Monadnock Mills, making Claremont one of the state’s premier manufacturing towns. Additionally, Tyler’s grandson, John Tyler, patented a highly sought-after turbine water wheel in 1850s that was sold to mills around the country.
Today, in New Hampshire, there are more than 60 hydroelectric facilities located in 18 towns and cities throughout the state, totaling around 50 megawatts, according to the Granite State Hydropower Association’s website. Those projects generate around 50 megawatts each year, enough to power about 35,000 homes. In Claremont there are two other small hydro plants on the Sugar River: one off Factory Street and the other along Plains Road.
King said the Claremont plant attracted his attention for two reasons: “I have always loved Claremont, from the first time I drove through here,” he said. “Beyond that, I know John Webster, a colleague.”
In addition to his engineering knowledge, King has also had to be a savvy businessman. He estimates that the investment so far is in the “hundreds of thousands” of dollars, so he’s eager to save money at every opportunity.
“There is no way you could do this whole thing economically if you went out and hired an engineer and bought everything new. Can’t do it. You have to be very careful with your expenditures.”
For example, when the shaft on one of the turbines had to be replaced, it became a creative do-it-yourself project. “There is so much force on (the gear box), if it bends it is tough on all the bearings inside,” King said. “So we took the old shaft, chopped it in half and we are making giant pusher struts to hold that gear box. It will keep the gear box from flexing. ... Again, buying something like that new, forget it.”
It’s Automatic
Another example of cost-saving is a sensor that will help automate the plant.
Under the previous ownership, King said everything was manual, requiring an operator to look at the river and decide how much power it could deliver. Now, he said, “We are automating the whole thing.”
The key to that is a sensor that grabs “every hunk of data in the plant.” King pointed to the small white box near the turbine. “So this guy, I just mounted yesterday. That measures how much the hydraulic cylinder opens and thereby how much the gates are open and thereby how much water you are using, and that feeds back to the computer.
“As is our style, that sensor, a $500 item, I got on eBay for $100.”
King has also spent a lot of time in a small room overlooking the turbine generators working on computer-related equipment that had to be improved to meet utility requirements.
“I spent months rebuilding all of this to bring it up to modern standards,” King said. “All this stuff is ... electrical protection. It shuts off the generators for electrical inconsistencies, like high and low voltage, high and low frequencies,” King said. “That is not the automation, that is the just protection the utility requires.”
In the same room is large industrial computer that was previously in use at a hydro plant in New York. King’s company had sold the plant and the new owners wanted to upgrade everything.
“They tore all this perfectly good stuff out and they gave it to us,” King said. “ ‘We don’t want it, you guys want it?’ ”
The computer sat in King’s basement until the Claremont plant was bought.
King is also installing software that will control everything about the plant through a computer. “And the really cool part is, through that modem and an old-fashioned landline, we can call the plant and control it and monitor it. And furthermore, it sends out text messages on any plant problems,” he said.
“Mostly it will be self-contained and the computer will run it. But we can monitor it, we can override the computer remotely, plus we will have a couple of local guys making daily visits. Once the thing is running, presumably we won’t be spending much time here.”
King’s enthusiasm for creating renewable power is apparent. “I love water,” he said while watching it crash over the dam. “It is clean. It is the original renewable. A great resource.”
Sam Payne, who was working with Taylor cutting away at the old shaft to create struts for gear box, was previously a circus acrobat, King said.
“He got too old for that and he has always had an interest in hydro. People get bitten by it and is hard to shake it.”
The business brings daily challenges that are always different.
“Having text messages coming from your automated plants, plant goes down at 2 in the morning, you are up and you are dealing with it,” King said. “We are always dancing around these five plants doing maintenance, capital improvements and so forth.”
Patrick O’Grady can be reached at pogclmt@gmail.com.